The Importance of Welding WPS: Ensuring Quality and Safety in Your Projects
Unlocking the Power of Welding WPS: Techniques for Efficiency and Safety in Fabrication
In the realm of fabrication, Welding Procedure Requirements (WPS) stand as the foundation of welding procedures, dictating the required steps for achieving both efficiency and safety in the manufacture procedure. Comprehending the ins and outs of WPS is vital to using its full possibility, yet several organizations have a hard time to open truth power that exists within these documents (welding WPS). By diving into the approaches that maximize welding WPS, a world of improved efficiency and heightened safety waits for those happy to check out the nuances of this vital facet of manufacture

Value of Welding WPS
The significance of Welding Treatment Specs (WPS) in the fabrication industry can not be overstated. WPS work as an important roadmap that details the required actions to ensure welds are performed continually and properly. By defining necessary criteria such as welding processes, materials, joint designs, preheat temperature levels, interpass temperatures, filler steels, and post-weld warmth treatment needs, WPS offer a standard technique to welding that enhances effectiveness, top quality, and security in manufacture processes.
Adherence to WPS aids in accomplishing harmony in weld quality, lowering the possibility of issues or architectural failings. This standardization additionally helps with conformity with industry guidelines and codes, ensuring that produced frameworks meet the needed security requirements. In addition, WPS documentation makes it possible for welders to duplicate effective welding treatments, bring about constant outcomes throughout different tasks.
Fundamentally, the precise growth and strict adherence to Welding Procedure Requirements are vital for supporting the stability of bonded structures, safeguarding versus possible dangers, and upholding the credibility of fabrication companies for supplying top quality items and solutions.
Crucial Element of Welding WPS
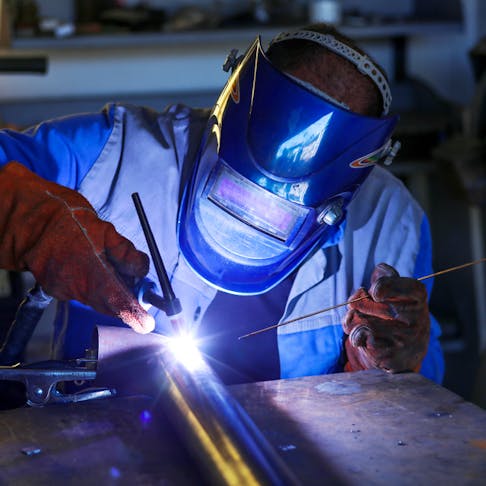
Enhancing Efficiency With WPS
When maximizing welding procedures, leveraging the essential elements laid out in Welding Treatment Specifications (WPS) becomes vital for improving procedures and making the most of performance. One method to boost performance with WPS is by carefully picking the ideal welding parameters.
Regularly assessing and upgrading the WPS to incorporate any type of lessons learned or technical developments can also add to effectiveness improvements in welding procedures. By accepting the guidelines established forth in the WPS and continually looking for ways to enhance procedures, makers can accomplish greater effectiveness levels and superior end results.
Ensuring Safety And Security in Fabrication

Security protocols in manufacture play a pivotal role in safeguarding employees and enhancing functional treatments. Guaranteeing safety in manufacture entails a complex technique that includes numerous aspects of the welding procedure. One fundamental element is the provision of individual protective equipment (PPE) tailored to the details hazards present in the manufacture setting. Welders should be geared check it out up with ideal gear such as helmets, gloves, and safety apparel to mitigate risks linked with welding activities.
Furthermore, adherence to proper ventilation and fume extraction systems is important in maintaining a healthy workplace. Welding fumes include unsafe compounds that, if breathed in, can pose severe health dangers. Carrying out reliable ventilation measures helps to minimize direct exposure to these hazardous fumes, promoting respiratory wellness amongst workers.
Routine equipment maintenance and inspections are likewise essential for making certain safety in manufacture. Malfunctioning machinery can result in crashes and injuries, emphasizing the significance of prompt repairs and routine checks. By focusing on safety steps and cultivating a culture of awareness, manufacture facilities can develop a secure and effective workplace for their workers.
Carrying Out WPS Finest Practices
To improve functional performance and ensure high quality look at this site results in manufacture procedures, incorporating Welding Procedure Spec (WPS) finest techniques is extremely important - welding WPS. Implementing WPS finest methods includes careful preparation, adherence to industry standards, and constant tracking to ensure optimum outcomes. Firstly, choosing the ideal welding procedure, filler material, and preheat temperature level defined in the WPS is important for achieving the wanted weld top quality. Second of all, making certain that certified welders with the essential qualifications accomplish the welding treatments according to the WPS standards is necessary for uniformity and dependability. On a regular basis assessing and upgrading WPS files to show any process improvements or adjustments in materials is also a crucial best technique to maintain precision and relevance. Additionally, providing comprehensive training to welding employees on WPS demands and finest practices cultivates a culture of safety and top quality within the manufacture atmosphere. By diligently applying WPS finest practices, producers can improve their operations, decrease mistakes, and provide superior items to satisfy customer expectations.
Conclusion
Finally, welding WPS plays a vital duty in ensuring efficiency and safety in fabrication processes. By concentrating on essential aspects, boosting efficiency, and executing finest techniques, firms can optimize their welding procedures. It is necessary to focus on safety and security measures to stop crashes and guarantee a smooth production procedure. By complying with these approaches, businesses can unlock the full potential of welding WPS in their construction operations.
In the realm of fabrication, Welding Procedure Specs (WPS) stand as the foundation of welding procedures, determining the essential actions for attaining both performance and security in the manufacture procedure. By specifying crucial criteria such as welding processes, materials, joint designs, preheat temperatures, interpass temperature levels, filler metals, and post-weld warm treatment requirements, WPS provide a standard strategy to welding that improves effectiveness, quality, and safety in manufacture processes.
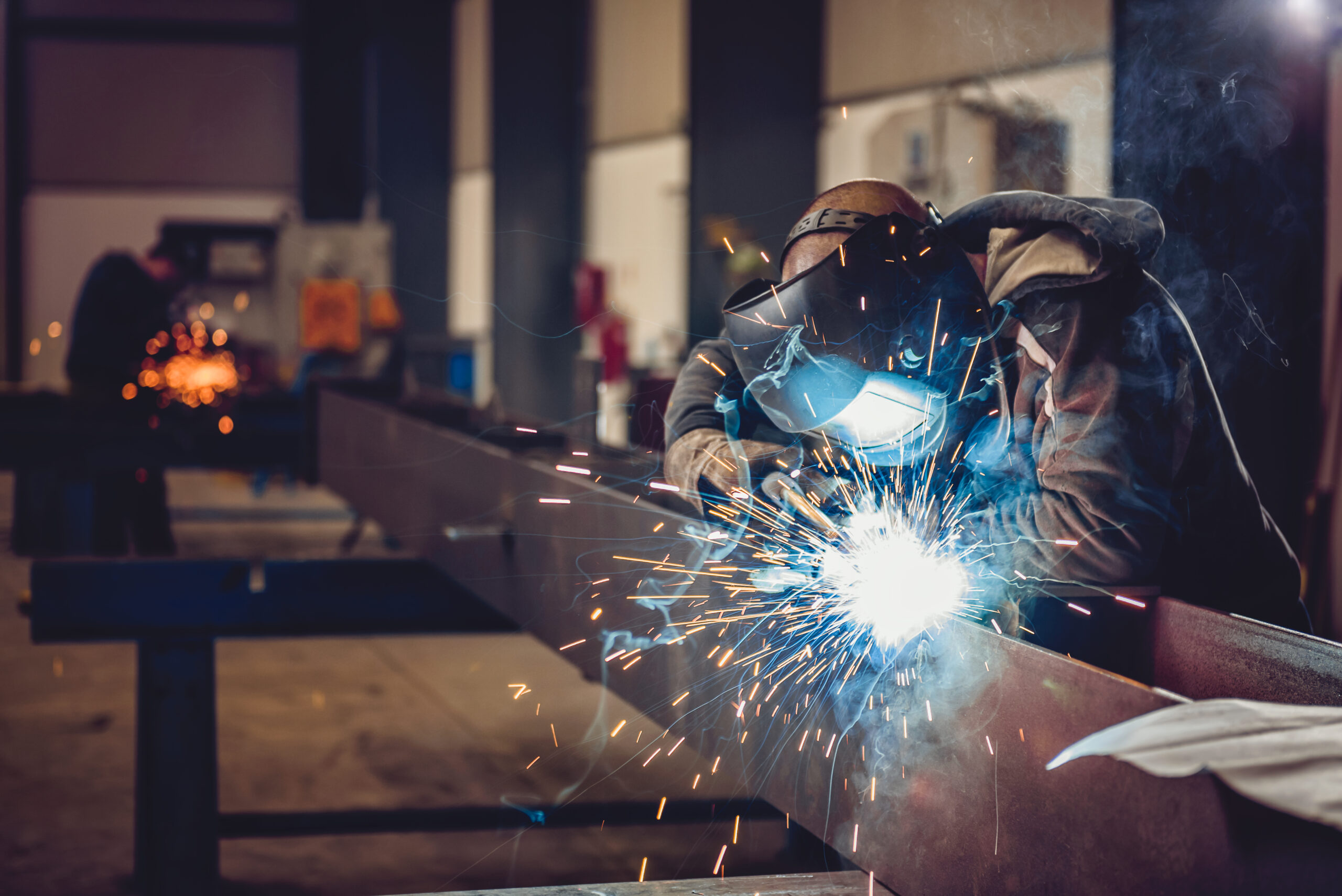
When enhancing welding procedures, see this website leveraging the essential aspects outlined in Welding Procedure Specs (WPS) comes to be vital for taking full advantage of and enhancing procedures productivity. (welding WPS)